Retrofit & Upgrade Kit
Retrofit & Upgrade Kit
Retrofit Kits for Vokes Stream-Line Transformer Oil Filtration Plants
For UK Built Vokes Stream-Line plant owners TFS offer complete servicing and refurbishment of your existing transformer filtration plants to bring them back to as new operating standards. We also have retrofit kits available to add additional features and functions to your existing Vokes Stream-Line units. These transformer filtration upgrade kits are designed and manufactured by our highly trained technical and engineering staff here in our Australian workshop.
Ask about our newly pioneered oil mist collection system, which is now included in all of new build plants, to minimise oil carry-over to the vacuum pumps while dehydrating the oil. This system can also be retro-fitted into existing Vokes manufactured plants.
Australian made Rugged Heater Vessels Replacements Retrofited into Vokes Stream-Line Transformer Oil Filtration Plants
For Vokes Stream-Line plant owners TFS offer our very own Australian Rugged Heater Vessel & Heaters to replace your UK built heaters.
Main Issues with UK heater vessels
UK designed Heaters blowing, cracking due to not handling transport on rough roads and also heater bobbins becoming brittle over time. To replace heaters with the UK heaters is extremely expensive and heaters have a long manufacture lead time as opposed our robust Australian heaters.
The Fix
Replace heaters with Australian manufactured heater elements. (Actual heater vessel will need to be replaced as well due to larger diameter Australian heater elements.)
Outcome,
The Outcome
A more robust heater vessel and elements which will not need replacing as often as they are made for our Australian conditions and roads, (and if they do they are a third of the cost and readily available). To date we haven't replaced or repaired any of the Australian manufactured heaters in over 8 years of supplying them.
The photos below show UK smaller more fragile heaters which break easier than our Australian made robust heaters, even the wires are twice the size of the UK heaters.
Australian Made MG Cartridge Filter vessel Replacements Retrofitted into Vokes Stream-Line Back-Flush filter Plants
For Vokes Back-flush filter Stream-Line plant owners TFS offer our very own MG range filter vessel to replace the out dated technology of the edge filtration.
We have listened to our customers with the Backflush filter system who are finding the edge filtration is failing over time and allowing particles through particularly as the filter packs age, they are finding the filters have extremely lengthy lead times and price are now to high due to the labour intensive production methods of these filters.
We have now completed many conversions to our upright disposable filter vessel with this being a more reliable cost effective method of filtering transformer oil.
We can even upgrade your SL20 (2000L/hr) to a 3000L/hr plant
Large capacity high efficiency oil trap
Situated between the vacuum pumps and vacuum chamber to minimise the carryover of insulating oil, protecting the vacuum pumps from oil flooding and minimising maintenance.
- Fitted with sight glasses to monitor level of collected oil
- Manually operated drain valve
High quality heavy duty canopys
Provides physical and environmental protection
- Multiple doors for ease of operation and maintenance
- All solid doors fitted with key locks
- Lift up solid doors fitted with gas struts
For jobs that are in tight spaces that side lifting doors are not an option;
We also supply a soft roll up side door canopy in either painted steel or Stainless steel with Side doors replaced with soft roll up doors providing physical & environmental protection complete with;
- Engineered lifting points
- Inbuilt LED Canopy lighting
- Multiple doors for ease of operation and maintenance
- All solid doors fitted with key locks and lift up solid doors fitted with gas struts
Integrated auxiliary vacuum pump for transformer evacuation
- Additional vacuum pump dedicated only for transformer evacuation (not required for the dehydration process)
- Various options available with capacities up to 1,200m3/h (integrated)
Self-contained standalone vacuum units are also available (500, to 2,500m3/h) if there is not enough room for an integrated vacuum pump – Contact us for details
6000 litre per hour Cartridge filtration plant with the additional 1000m3/h capacity integrated vacuum pump fitted
Hydraulic Hoses
For quieter, more efficient and leak free operation. We use engineered hydraulic fittings to achieve a perfect seal as opposed to old fashioned copper fittings which were designed generally for water in a stationary position and which commonly vibrate loose constantly causing vacuum leaks which leads to foaming and other operational issues.
Hoses
- Wire reinforced composite oil hoses available in different lengths.
- We can replace your existing plants copper pipes with our new Hydraulic hoses
Fullers Earth Deacidification Connection kits
Our Deacidification units use Fullers Earth and have been developed to be utilised in conjunction with our Insulating Oil Treatment Plants to enable operators to regenerate their own oil. If your current plant doesn't have the connection assembly we can retro fit this to your existing Filter Plant.
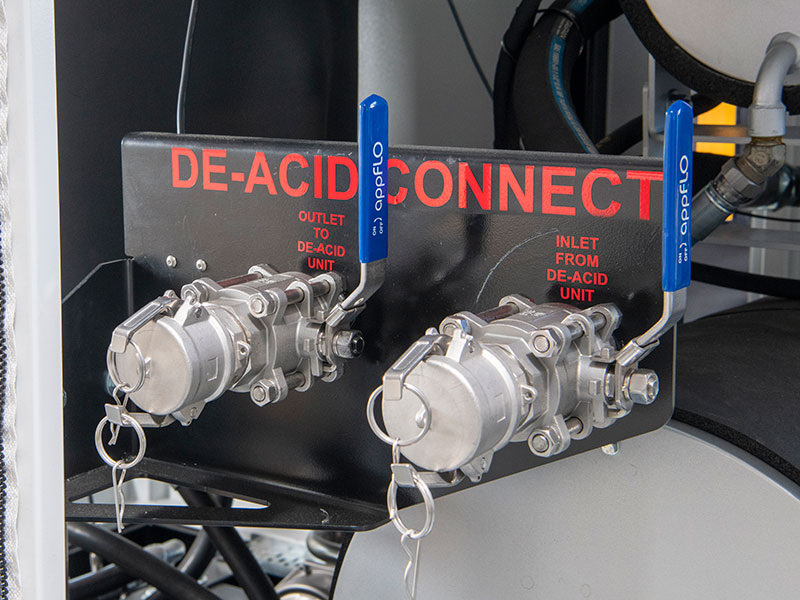
Staged Heater Loading - Now available as a retrofit kit
The majority of the electrical load from a Vokes Stream-Line insulating oil treatment plant comes from the electrical heater which uses thermostatic control to maintain the oil at a preset temperature. The thermostat switches all the heater elements simultaneously in response to demand.
We have received feedback from users that this high instantaneous electrical loading can result in problems when plants are run from diesel generator sets, with reports of the generator's overload protection tripping dropping supply to the plant. Users have also reported the high instantaneous loading causing noticeable and frequent stress to the generator in response to demand from the thermostat.
This issue is more evident when the capacity of the generator set is close to the overall electrical requirement of the plant, and/or with older generators, or when using generators with sensitive or incorrectly set overload protection.
In response to customer feedback, all new insulating oil treatment plants will be fitted with staged heater loading so that in response to demand for heat, the heater load is switched in two or three equal stages (depending on plant model and heater size), with a timed delay between each stage, to allow recovery of the generator set between each stage of the loading.
This staged loading avoids spurious tripping of generator sets, with loss of plant operation, and is also 'kinder' to generators and engines, resulting in less wear and tear.
This improvement of staged heater loading is now available as a retrofit kit, supplied with instructions, for easy installation by a competent electrician. Alternatively the modification can be carried out in our own workshop.